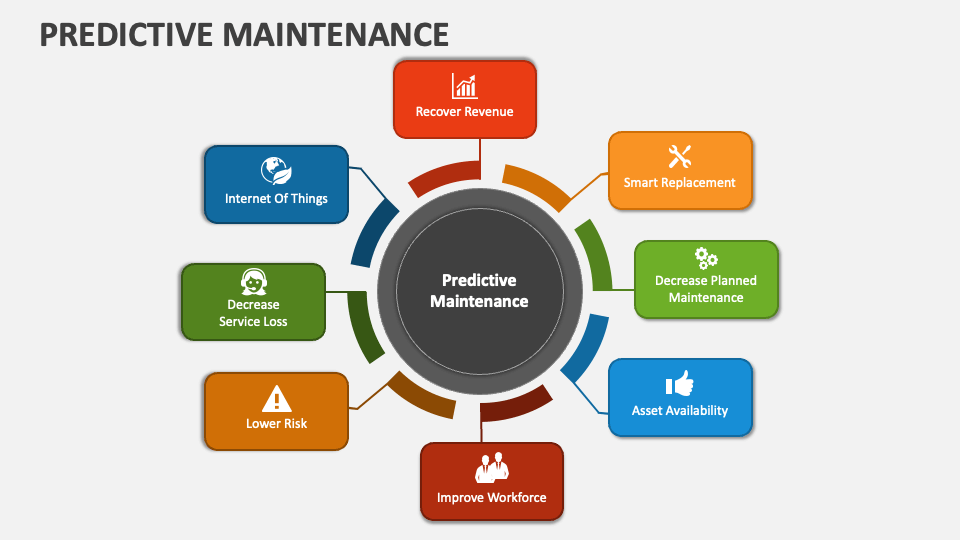
Status: Summary of Final Blueprint
Author: Shahab Al Yamin Chawdhury
Organization: Principal Architect & Consultant Group
Research Date: October 9, 2024
Version: 1.0
1. The Challenge: The Predictive Maintenance Paradox
For years, traditional predictive maintenance (PdM) based on machine learning (ML) has been a cornerstone of Industry 4.0. While effective at detecting anomalies from sensor data, these systems have hit a wall. They operate in a “data-rich, insight-poor” environment, generating a high volume of vague alerts (e.g., “Vibration Anomaly”) without the necessary context to guide action.
This leads to significant operational friction:
- Alert Fatigue: Technicians are overwhelmed by notifications, leading them to mistrust or ignore critical alerts.
- Decision Latency: Each vague alert requires a slow, manual investigation, forcing experts to sift through siloed knowledge sources like OEM manuals, repair logs, and service bulletins.
- The Knowledge Silo Problem: The core issue is architectural. The ML models analyzing sensor data are disconnected from the unstructured human knowledge needed for true diagnosis. This forces human operators to manually bridge the gap between the machine’s alert and the organization’s collective expertise.
Maintenance Strategy | Core Principle | Key Drawback |
Reactive | “Run-to-Fail” | High cost of unplanned downtime. |
Preventive | “Time-Based” | Can lead to unnecessary maintenance. |
Traditional PdM | “Condition-Based” | Vague alerts, slow decision-making. |
GenAI-Enhanced PdM | “Context-Aware” | Higher initial tech integration cost. |
2. The Solution: The GenAI Intelligent Context Layer
Generative AI provides the solution by augmenting—not replacing—existing PdM systems with an intelligent “context layer.” This new architecture automates the diagnostic process that is currently manual and slow.
Core Components:
- Retrieval-Augmented Generation (RAG): This is the bridge to reality. RAG connects the AI to an organization’s specific knowledge base (manuals, logs, reports). It retrieves the most relevant, factual information in real-time, grounding the AI’s responses in verifiable data and preventing “hallucinations.”
- Large Language Models (LLMs): These are the engines of understanding. After RAG retrieves the facts, the LLM synthesizes the disparate pieces of information into a coherent, human-readable narrative, generating summaries, probable causes, and step-by-step recommendations.
- AI Agents: These are the engines of action. Triggered by an ML alert, an AI Agent autonomously orchestrates the entire workflow. It queries the RAG system, passes the context to the LLM, and curates the final, context-rich recommendation for the technician, turning hours of investigation into seconds.
This architecture transforms the system from an opaque “black box” into a transparent “glass box,” as the AI can cite the sources for its conclusions, building essential trust with frontline users.
3. New Capabilities & ROI
The GenAI layer unlocks capabilities far beyond simple alerts, fundamentally changing the nature of maintenance.
Key Capabilities:
- Automated Root Cause Analysis (RCA): Instantly analyzes historical data to identify the most likely root causes of a failure, supported by evidence.
- Dynamic Work Order Generation: Automatically creates comprehensive work orders, including parts lists, step-by-step instructions, and safety procedures.
- Living Knowledge Systems: Transforms static manuals into interactive experts that technicians can query with natural language, democratizing expertise.
- Synthetic Scenario Modeling: Generates realistic failure data for rare events, allowing ML models to be trained for scenarios they have not yet encountered.
Measuring the Transformation:
The business case is measured by improvements in traditional KPIs and a new, GenAI-specific metric.
- Mean Time To Repair (MTTR): Drastically reduced by cutting diagnostic time.
- Mean Time Between Failures (MTBF): Increased through more precise, proactive interventions.
- Overall Equipment Effectiveness (OEE): Boosted by minimizing unplanned downtime.
- Mean Time To Insight (MTTI): A new KPI measuring the time from alert to actionable insight, directly quantifying the efficiency gain from GenAI.
The ROI is driven by reduced downtime, lower maintenance costs, optimized MRO inventory, and extended asset lifespan. Strategically, the system creates a permanent “Knowledge Asset,” mitigating the risk of knowledge loss from an aging workforce.
4. Strategic Implementation & Future Horizon
A disciplined, phased approach is essential for success.
Phased Implementation Roadmap:
- Phase 1 (Months 1-3): Foundational Assessment & Data Strategy. Prioritize critical assets and audit data infrastructure.
- Phase 2 (Months 4-9): Pilot Program. Deploy a RAG-based knowledge retrieval tool for a small group to demonstrate value and build trust.
- Phase 3 (Months 10-18): Scaling with Agentic AI. Introduce AI agents to automate the diagnostic workflow from alert to work order.
- Phase 4 (Months 19+): Enterprise Rollout & Evolution. Scale the solution and establish a Center of Excellence (CoE) for continuous improvement.
The Future Horizon:
This initiative is the first step on a path toward fully autonomous industrial operations.
- Near-Term: Agentic AI will handle autonomous scheduling, dispatch, and supply chain integration.
- Mid-Term: GenAI-powered Digital Twins and Embodied AI (robotics) will converge the virtual and physical worlds, allowing for risk-free simulation and automated physical repairs.
- Long-Term: The ultimate goal is the creation of self-healing machinery, where AI and smart materials enable assets to intrinsically repair damage, moving maintenance from a task to an inherent property.
C-Suite Action Plan: Leadership must act now by establishing a GenAI task force, launching a focused pilot, and developing a long-term talent and governance strategy to navigate this transformation.